Wood Deck Stains:
Low-VOC Paint
Low-VOC Paint. What does that mean for contractors who stain and maintain decks? It could mean a lot — especially in time. New product designs compliant with the low-VOC regulations often have different application properties and performance characteristics.
by Susan Brimo-Cox
In many parts of the country this means a busy season of business as usual. But in the Mid-Atlantic region this year, deck painting contractors are learning some of the lessons that contractors in parts of California and Arizona worked their way through several years ago.
Ozone Transportation Commission (OTC) guidelines specifying stricter volatile organic compound regulations became effective January 1 in New York, New Jersey, Pennsylvania, Delaware, Maryland, the District of Columbia and northern Virginia.
If you are not affected yet by such rules, just wait: you may be soon. Other states and regions are looking into revising architectural and industrial maintenance (AIM) paint and coating rules, including several states in New England, such as Maine, New Hampshire and Massachusetts.
The Rohm and Haas Paint Quality Institute’s John Stauffer reports that while New England states have not yet implemented new regulations, New Hampshire has published a new AIM rule. And he sees the trend moving to the Midwest, too. “States now considering OTC-like AIM rules include Wisconsin, Illinois, Indiana, Michigan, Missouri and Ohio.” (The Lake Michigan Air Directors Consortium is planning a public workshop in June.)
By the end of the decade, much of the country may be working under new VOC regulations. Stauffer points out that the National Paint and Coatings Association is projecting that by 2008-2010 more than two-thirds of the country would be covered by an OTC-type AIM rule, and an OTC-type rule may replace the current national AIM rule everywhere except in California by 2010. In addition, he says, Canada is looking at implementing a national AIM rule patterned after the OTC rule.
What does that mean for contractors who stain and maintain decks? It could mean a lot — especially in time. New product designs compliant with the low-VOC regulations often have different application properties and performance characteristics.
As Jake Clark, owner and president of Armstrong-Clark Co., succinctly puts it, “You can’t blow and go with all low-VOC deck products.”
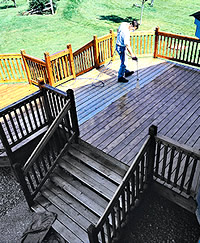 |
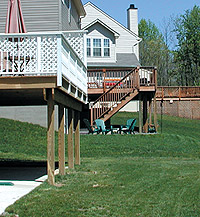 |
Careful spraying avoids lapping problems when doing a deck. |
Low-VOC chemistries differ
Tom Daniels, vice president of sales at Samuel Cabot Inc. understands the concerns of contractors regarding the changing VOC regulations. “The biggest issue is communication and the misunderstandings and misinformation that are prevalent anytime there is change,” he says. “Today’s low-VOC products are not better or worse than the products they are replacing.” However, they are different. The chemistries of low-VOC products essentially differ from traditional products in one of two ways, explains Gary Finseth, vice president of marketing for The Flood Co. In some instances, the oil-based versions are modified to have higher solids and less thinner. This results in a lower VOC, he says, but “these modified formulas are more costly and have different application characteristics.” The second method is a totally different chemistry that employs water-based resin systems — with potentially less robust application and performance, he says. Daniels points out that some low-VOC products may be formulated with solvents that are clean-air friendly, and hence exempt from the VOC calculations. Researchers continue to seek other ways to accomplish adequate performance with reduced-VOC alkyd products. According to Stauffer, the most challenging areas are clear and lightly pigmented coatings. For solid-color deck stains, compliant water-based products have been available, he says. But semi-transparent stains are a challenging area for oil-based products. “Compared with traditional oil-based semi-trans stains, the water-based products are not so forgiving when it comes to lapping properties, so care is required in order to get a uniform appearance,” he explains. As with any reformulating, this is an evolving process. Manufacturers are either working with their current raw material suppliers or investing their own R&D dollars to develop proprietary technology, especially when it comes to resin, reports Steve Revnew, director of architectural marketing, residential segments at Sherwin-Williams. The cost per-gallon of these new products is greater, he says, because of the resources required to develop this unique technology and because in many cases the solids of the products are increased. On the other hand, he says, the new technology significantly reduces labor cost because fewer coats are required. Ron Boyajian, product-marketing manager at Massachusetts-based California Paints, points out that many manufacturers have been working in advance of the low-VOC changes. But there’s another issue, as well: maintaining dual inventory for compliant and non-compliant states. “But the good thing is currently the regulations allow for selling through — allowing retailers to sell out of a former product that’s already in stock, as long as it was manufactured before the new regulation went into effect.” Manufacturers are also making decisions regarding which older formulas to supply in smaller containers, Stauffer reports, since containers smaller than one gallon are exempt from the new OTC rules. |