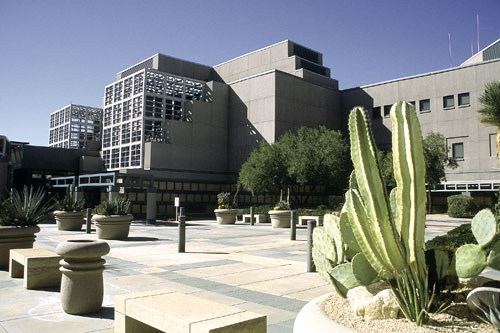
Masonry and Concrete
Coating Innovations
When coating masonry substrates, you may be dealing with tilt-up, precast or poured-in-place concrete; stucco, cinder block or CMU, cement, brick or plaster. Read on for tips on choosing and applying long-lasting finishes on masonry surfaces.
by Pete Donati
unique challenges you're likely to face when it comes to coating options. To begin with, the term masonry covers a lot of ground. On any given job, you could be dealing with tilt-up, precast or poured-in-place concrete; stucco, cinder block or CMU, cement, brick or plaster, among others. And the list of characteristics that accompanies the various masonry substrates can leave you wondering where to start.
But with a little knowledge, preparation and a systematic approach to choosing and applying coatings, you'll be able to create long-lasting finishes on any type of masonry you're likely to encounter.
When dealing with concrete and masonry substrates, selecting the proper coating should first focus on the result you want to achieve. For example, determine if a smooth or textured finish is desired. Would a bright, intense color fit in best with the surroundings, or would your customer prefer a more subtle shade for curb appeal? Next, take into consideration the condition and characteristics of the particular type of masonry you intend to coat. Are you dealing with new construction, or a deteriorated or dirty existing structure? How much of a factor is moisture or severe weather, particularly in the form of wind-driven rain? How porous is the substrate? Are there cracks or surface irregularities that need to be camouflaged? The answers to all of these questions will factor heavily in coating selection.
As with any coating project, surface preparation is the key to a durable, quality finish. When preparing to paint concrete and masonry, it's very important to remove all contaminants or loose debris on the surface of the substrate before applying any coatings. Starting with a clean, dull and dry substrate will go a long way toward achieving the desired results and reducing callbacks.
Power wash or clean the dirt, mildew or loose powdery material from the surface thoroughly without adding to any existing damage in the process. If there appears to be dirt present even after washing, chances are there is mildew on your substrate. If so, scrub it with a solution of one part bleach and three parts water. After scrubbing, allow the solution to stand on the surface for 10 minutes and then rinse the surface thoroughly. It's best to let the surface dry for 48 hours before you begin painting.
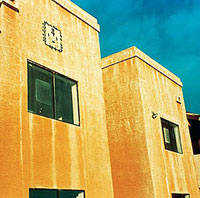 |
Burning: Surfacers are formulated to prevent breakdown of the paint
binder, which results in permanent discoloration, or burning, of the
paint film. When choosing a surfacer, be sure to select one that has
a high pH resistance since new masonry can have a pH as high as 12-14. |
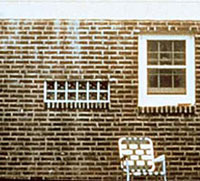 |
Chalk Run Down: Chalk run down can best be prevented by treating
fresh concrete with a 100 percent acrylic conditioner that seals the
surface and prevents adhesion problems and delamination. |
It's always a good idea to use a primer to ensure topcoat adhesion. Primers also cover a multitude of sins including stains and discoloration, surface marks and previously applied coats of deep, bright or vivid colors.
Acrylic masonry primers are recommended for cementitious panels, brick, concrete and stucco because they deliver high film-build and increase topcoat durability. If your surface is routinely subjected to extreme weather, an acrylic primer will take care of surface issues as well as reinforce the topcoat against moisture.
High performance acrylic primers are also your best choice when working with masonry substrates with a high pH level. If you select a product that can be applied to surfaces with a pH level of up to 13, you'll save yourself the hassle of dealing with efflorescence later. Efflorescence refers to the deposits of soluble salts that form on the surface of the substrate when moisture migrates from the concrete or brick substrate. Another advantage of acrylic primers is that they can be applied after just a seven-day cure, which makes the most of your application time.
Porous masonry substrates are another matter entirely and require a different type of base coat. When prepping concrete block, porous cement or brick, you'll want to prime the surface with a block surfacer or filler. Premium concrete block surfacers are made of acrylic latex resin and are the best way to cover a rough, uneven profile. These coatings create a solid barrier between the topcoat and the substrate; fill pores, voids and pinholes; and provide a stable, smooth foundation for finishing. They also reduce topcoat consumption.
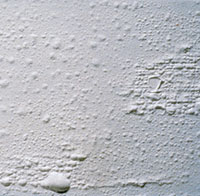 |
Blistering: Moisture penetration is the most common cause of blistering
when it comes to masonry substrates.
Elastomeric primers are the best way to combat this problem on above-ground
surfaces because they resist wind-driven rain and other severe weather
while releasing moisture vapor and maintaining adhesion. |
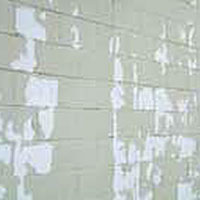 |
Peeling: Acrylic primers are recommended for brick, concrete and
stucco because they deliver a high film build, increase topcoat durability
and protect against moisture penetration. |
Surfacers are specifically formulated for application on freshly cured (typically seven days) or high-alkaline mortar without resulting in mortar burns or delamination. Alkali burn occurs when new masonry with a pH of 12-14 causes breakdown of the paint binder, which results in deterioration and permanent discoloration of the paint film.
With today's advanced technology, block surfacers are available in light-weight formulas that can be used on low-temperature installations to cut down on application time and labor costs. Again, choose a product that has a high pH resistance to reduce the possibility of defects or callbacks.
Conditioners can be particularly helpful when you're covering poured-in-place and tilt-up concrete, stucco and brick or an existing deteriorated topcoat. They bond light chalk, old paint and dusting concrete, which prevents adhesion problems and delamination. One hundred percent acrylic conditioners offer excellent durability and weathering. Conditioners have a low film build that penetrates deeply to bond chalky substrates and adhere to high pH levels, and they also have the benefit of being a little more economical than high-build acrylic primers. On fresh concrete, a conditioner makes a great sealer that can shorten cure time from 30 to seven days.
We've all seen the blistering, cracking and peeling that results from moisture penetration. It's probably the most common issue you'll encounter with concrete and masonry coatings. Some typical water problems include dark areas due to dampness, water leakage from wind-driven rain and of course, mildew. When the job calls for a waterproofing system, go with an elastomeric primer and topcoat system that will repel exterior moisture and allow moisture vapor to escape. Elastomerics are made for above-ground concrete and masonry, and the best ones include acrylic binders that maintain flexibility for years.
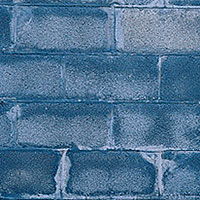 |
Efflorescence Gray: Acrylic primers help avoid efflorescence, the
build up of soluble salts on masonry surfaces, because they prevent
moisture from penetrating the substrate. These flexible coatings can
also be applied after just a seven-day cure, which minimizes time on
the job.
|
These coatings produce a thick and elastic film, which hides hairline cracks, patches and other surface irregularities. Some elastomeric coatings are VOC compliant, and in addition to being a waterproofing system, they prevent the penetration of damaging atmospheric elements such as dirt, carbon dioxide and salts. The major benefit of elastomeric coatings is that they increase the life of concrete and masonry by providing protection from wind-driven rain — even in coastal or severe-weather environments — and release moisture vapor while maintaining surface adhesion.
In certain climates water penetration problems are compounded by the cracking that results in concrete and masonry from freeze-thaw cycles. Elastomerics are perfect for such environments because of their ability to expand and contract without wrinkling or cracking. The flexibility built into elastomerics makes them stretch over the problem area and return to their original appearance when the surface contracts. Be aware that cracks in stucco will telegraph through the topcoat, so they must be repaired with patches and sealants before you consider repainting.
Using a textured elastomeric topcoat is another option when covering surface imperfections. As well as providing waterproof protection, textured elastomerics can minimize minor cracks or patches, improve the look of tilt-up concrete and match existing textured surfaces.
Elastomerics are perfect for such environments because of their ability
to expand and contract without wrinkling or cracking. |
It's often thought that the only way to improve the look of concrete is through time-consuming and expensive methods of acid etching, color admixtures and overlays, but concrete stains have changed all that.
Instead of chemically reacting with the cement mixture, concrete stains are spray applied and penetrate deeply into the concrete surface, which creates excellent adhesion on new and old concrete. Concrete stains are well-suited for use on pre-cast tilt-up concrete and above-grade concrete walls in either smooth or textured finishes. They provide uniform color, resist fading and efflorescence, are water repellent and allow for the release of moisture vapor. There are concrete stains available that comply with the strictest air quality regulations due to their very low VOC content.
Significant strides have been made in creating advanced masonry coatings. Specifying coatings for this often challenging substrate requires paying particular attention to the desired aesthetics, surface preparation and product knowledge. Once you've mastered those elements, you'll be able to satisfy your customers with durable finishes that offer good looks as well as protection.
Pete Donati is director of marketing, commercial segments, at The Sherwin-Williams Company in Cleveland, Ohio.

|