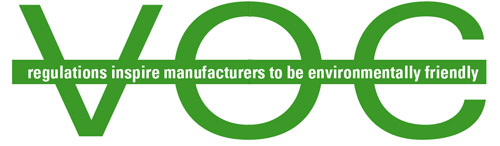
Low-VOC Coatings
Low-VOC regulations in architectural coatings are driving technology and contractors to be environmentally-friendly.
by Susan Brimo-Cox
What’s driving the push to reduce them in architectural coatings?
The primary reason for the VOC pressures are macro air pollution issues in various regions of the country, reports Steve Sides, vice president of the National Paint & Coatings Association. Many industries are being affected in different ways as local and regional regulators tackle auto emissions, smoke stack gases, and paint products, to name a few. And a variety of consumer products, like shoe polish and hair spray, are feeling the pressure, as well, Sides says.
“This push is coming because regulators want to get a handle on overall air pollution,” Sides explains.
Other pressures are coming from the green building scene. Energy savings, resource conservation, indoor air quality, these are all aspects of a movement that promotes environmentally-friendly building. While not as strong a pressure as clean air, it continues to grow, and programs such as the U.S. Green Building Council’s LEED rating system (Leadership in Energy and Environmental Design) are pushing the concept more into the mainstream.
Matt Crawford, architectural services representative at Kelly-Moore Paint Co., observes, “The LEED program is a dominant program that owners and architects are leaning towards using.”
Sides agrees, “The environmental preference—the green quotient—is growing, and it is a very dynamic situation.”
Low-VOC regulations began to take hold in California in the 1980s, and the federal government followed along by passing initial EPA VOC limits in 1999. Since then stricter limits have been enacted by numerous states. VOC recommendations developed by the California Air Resources Board have served as a template for many states in New England and the Mid-Atlantic region. States in the Great Lakes region and the Midwest also are considering enacting stricter regulations, as is Canada.
But, no matter if you live in a state with stricter VOC limits or not, you are being impacted, and many industry insiders say it’s not a bad thing.
“There is some anxiety out there about low-VOC coatings, but mostly around change,” says Stewart Williams, technical director at Rohm and Haas’ Paint Quality Institute.
Contractors who are used to certain coating products and application techniques may not want to switch. However, these individuals are missing out on improved products.
Sides points out, “There are a lot of emerging technologies in architectural products to meet performance requirements as well as environmental constraints.” And, he says, there seems to be significant interest from coatings manufacturers to develop products to meet green standards.
Steve Revnew, director of marketing for Sherwin-Williams, says new technologies are actually a win-win for contractors. Oil-based and alkyd-based products were used years ago because the technology wasn’t yet available for water-based products. Now, water-based technologies offer a lot of advantages.
Water-based products have a few issues
In talking with manufacturers and contractors, the issues raised most often regarding water-based products are important to know, but are not prohibitive. In fact, water-based products have been around for some time now and contractors who use them regularly don’t even consider these issues a problem anymore.
Problem one: Older, solvent-based products were thinner and they penetrated the substrate better. Perhaps that’s true. But, as Revnew points out, solvent-based products also tended to drip—they were messier. Water-based products, on the other hand, are thicker and stay on the brush or roller.
Problem two: Water-based products raise the grain of wood. Improved water-based technologies have made this a non-issue.
Problem three: Some low-VOC paints don’t meet traditional freeze-thaw standards. In cold climates more care has to be taken to preserve the paint, but technology is advancing in this area. Crawford reports some exterior acrylic paints can handle temperatures down to 35 degrees Fahrenheit.
Problem four: Water-based paints have less open time and dry faster than traditional solvent-based paints. The key challenge here is to minimize the number of starts and stops to minimize lapping issues, but it can be done.
Problem five: Water-based paints don’t flow and level like solvent-based products. Revnew says paint manufacturers work side-by-side with sprayer and applicator manufacturers so they have the right equipment to go with any given product.
Crawford points out, “Resin technology has come a long way to improve water-based paints—better adhesion, color retention, durability, and flexibility, along with improved application characteristics. As research and development continues in this field (resin technology), water-based paints will also continue to improve.”
And don’t forget the easy clean up. It’s one of the most frequently noted advantages to using water-based paints.
One contractor’s perspective
Nigel Costolloe, president of Catchlight Inc. Fine Residential Painting, finds himself in an interesting spot. He is a painting contractor in Massachusetts, a state that has not yet adopted the low-VOC Ozone Transport Commission regulations, surrounded by states that have. While not directly affected by low-VOC regulations, he is indirectly affected in many ways.
Costolloe explains that paint manufacturers will not keep making boutique products for small markets. “New formulations designed for California and OTC are being applied across the board. So, even though Massachusetts hasn’t signed on, we will wind up with the same paints sold elsewhere.”
While Costolloe admits techniques he used for older paints don’t transfer to new products, he says you can teach old dogs new tricks. “You get used to the new material over time.”
In many ways the new low-VOC products are turning out to be a benefit to his company, he says. “We stress workplace safety in all we do. Low-VOC products fit right in with this philosophy.” Solvent-based products on a job site act much like second-hand smoke—you don’t have to be the one applying the paint to be affected by the hazardous fumes—plus, he explains, clients can occupy the space faster. Clean up also is much simpler and less expensive since he is not dealing with hazardous wastes. And his preference to use LEED-certified paints wherever possible has become a successful marketing strategy.
“LEEDs has taken a niche and made it standard. It’s the cutting edge of building and remodeling that’s driving the transition and driving the technology,” Costolloe explains. “The evolution to green paints is upon us, and it’s inevitable.”
What lies ahead?
Development of newer, better performing water-based technology is leading the reformulation of solvent-based products, and, in general, interior products are moving ahead faster than other categories. As Revnew emphasizes, “There is some reformulation in some products, but, from our perspective, we’re looking for new product designs to solve challenges.”
Durability and washability are two significant areas in which new low-VOC interior paints are really improving.
Williams agrees that from a low-VOC standpoint, water-based technology is ahead of traditional solvent-based technology, nonetheless, he adds, “as new, stricter regulations come into play even water-based products will need adjustment.”
Indeed, many water-based products contain some solvents, and zero-VOC products may contain VOCs up to 5 grams/liter.
In addition, there are some architectural paint product categories that still face strong challenges, among them stains and lacquers.
Regarding lacquers, Crawford reports lacquer formulation changes to meet 550 VOC grams/liter and 275 VOC grams/liter regulations have changed how these products are applied and special training is given to introduce these techniques.
As for stains, Williams observes, “From a performance standpoint, despite advances in water based technology, the stain product category has remained dominated by solvent base technology. This is a direct consequence of the unique balance in key application (e.g. lapping) and failure mechanism (e.g. flaking vs. erosion) in this category. Further regulatory restrictions or further advances in water-based technology may shift this in the future.”
Jake Clark, president of Armstrong-Clark, a stain manufacturer, says the evolution of a stain product to meet strict California regulations has been a challenge. He recalls, “In the old days, it was called ‘blow and go.’ You knew a stain would soak in. That’s not true anymore.” He observes that simply reducing the solvent content results in thicker stain products that require extra care in application and the wiping up of puddling; characteristics not enjoyed by contractors. Clark’s company—and others—are viewing these regulation challenges as opportunities to reformulate and introduce new products that work better in different ways.
From the manufacturers’ standpoint, investing in research and development is paying off. As Revnew points out, “Our target is always the most stringent regulation. From a supply chain standpoint, it doesn’t make sense to have multiple formulas out there.”
Other manufacturers have the same philosophy. And that’s really the bottom line of how the lowest-VOC regulations affect everyone.
As to the rationality of bucking change, low-VOC paints are not the first unpopular change introduced in the industry. As Costolloe points out, when the paint roller was introduced it was lambasted because it dramatically increased productivity, and people complained when lead was removed from paint.
Productivity turned out to be a good thing. So did removing lead. Maybe in 25 years or so the same thing will be said of low-VOC paints.
For more information about low-VOC regulations, see the Business Strategies section in this issue.

|