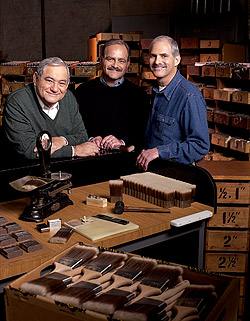 |
The Corona Brushes managing group of Gregory, Ben and Albert Waksman (left to right). |
Corona Brushes Inc.,
Tampa, Florida
Add a bit of black for a touch of class.
by David Thompson
. So when the Bolsheviks seized power after
World War I, he bid farewell to his Mother Russia and set out to make a new life in the West.
He left behind his wife and daughter until he could save enough money to send for them. But he brought with him a knowledge of how to process boar bristles to make paintbrushes — an Old World skill that would become the underpinning of his success in the New World. It would lay dormant for several years before he found a use for it.
Waksman hoped to settle in the United States, but with immigration quotas as they were, the closest he could get was Cuba.
“Little did he know he would be landing in a country that would become the first Soviet stronghold in the Western Hemisphere, 40 years later,” says Ben Waksman, one of two grandsons who joined the family business and are now vice presidents.
Jude Waksman went to work in Cuba as a laborer, eventually sending for his wife and child, then adding two boys and another girl to the family.
It wasn’t until World War II that Waksman’s insight into the way of the bristle would prove useful. With the war disrupting American paintbrush manufacturers’ supply of China bristle and Russian bristle, Waksman created a processing facility outside Havana to supply them with Cuban bristle. Adapted to a tropical climate, the Cuban hog produces a coarser bristle than its Chinese and Russian counterparts. But in a pinch, the Cuban import did the trick. After the war, Waksman’s bristle processing plant evolved into Corona Brushes, which, with the help of his two teenage sons, Gregory and David, grew into a major supplier of brushes and rollers throughout the Caribbean. Then came 1959 and the Latin American equivalent of the Bolshevik Revolution. Fidel Castro came to power, and two years later, the Waksmans were on the move again. “Castro was taking absolute control, and the Waksmans were part of a wave of over a million Cubans who left,” says Ben Waksman. “I was nine at the time. My brother was five.”
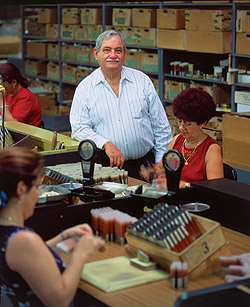 |
Quality brush making at Corona under the watchful eye of company president Gregory Waksman. |
This time, the U.S. welcomed the Waksmans with open arms.
Starting from scratch, they reopened Corona Brushes in a 500-square foot factory in an old part of Tampa, Florida.
“My grandfather wasn’t in the greatest of health then, so it was really up to my dad and uncle to get the business off the ground in the United States,” Waksman says.
“It was touch and go for a few years,” he says. “When you are really trying to establish a brand with quality rather than price, it’s hard to get recognition. Especially when you don’t have the funds to advertise or buy the latest technology or equipment. So they had to improvise and make a lot of personal sacrifice to ensure survival.”
Corona did survive, distinguishing itself by making a wide variety of professional-quality brushes and rollers handcrafted from the best materials available.
“We put effort into creating painting tools for the painter that will save him time and money, not by creating a cheap product, but by creating a product that will give him more production, more coverage per dip, fewer trips to the bucket, and more time on the painting surface,” Waksman says.
The hallmark of the Corona brush is its super-sharp chisel, which is set by hand at the base rather than created by clipping the tip of the brush with a machine. Hand-setting the chisel preserves the flagg of the bristle, providing a brush that cuts sharply and lays down smoothly from the first dip into the bucket, with no breaking-in time required.
Every paintbrush in Corona’s professional line, from the one-inch trim tool to the six-inch wall brush, has this handmade chisel.
There are other hand processes that go into making a Corona brush as well, nine in all, including boiling the natural bristle in-house, just as Jude Waksman had always done.
“At one time these hand processes were done by a lot of manufacturers, but they were abandoned over the years,” Ben Waksman says. “We have maintained the traditions but found ways to do them more efficiently.”
With today’s paints thicker than those of yesteryear (thanks to low VOC regulations and to the resins manufacturers add to water-based paints to get the look of a solvent-based finish), a high-quality brush with a good chisel is as important as ever.
“Newer paints don’t allow you to do a lot of back-brushing,” Waksman says. “You basically have to put it on and leave it alone. The Corona brushes allow you to put it on and lift off the surface and not leave brush marks.”
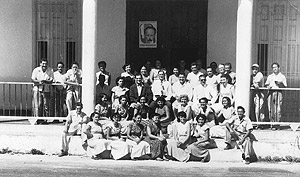 |
Original Corona Brush factory in Cuba, 1953. |
Corona relies mainly on independent dealers to sell its brushes, not national chains. “An Ace Hardware here and there might have Corona if it’s got a good paint department, but generally it’s your independent paint decorating center or regional paint manufacturer with their own paint store,” Waksman says. “We’ve kept it that way because we wanted to stay a professional house, we wanted to stay a handmade house and we wanted to control our destiny.”
That destiny led from the original 5,000-square-foot facility to a facility with triple the space five years later — and then to the company’s current Tampa location, which, after two expansions, has 70,000 square feet. The company has almost 100 employees, and it’s growing. Finding good employees can be a challenge, Waksman says. “It’s not that easy to get an employee who can learn how to make product manually anymore,” he says.
Jude Waksman has passed away, as has his son David. Jude’s son Gregory is president of the company, with grandsons Albert and Ben involved in all aspects of its day-to-day operation.
“The traditions of the family are very important,” Ben Waksman says. “Our father grew up in the business, and a lot of things he learned were handed down to us. And of course, as new materials come into play — the first synthetics in the 50s and 60s, polyester in the 70s and later Chinex in the 90s — we apply to the new materials the same traditions of quality.”

|