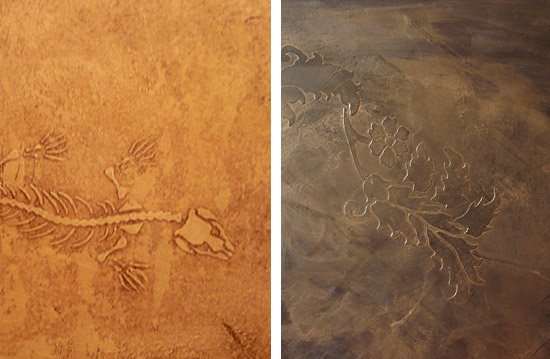
Decorative Plasters
Decorative plasters span a variety of diverse designing needs. Decorators discuss the difference between traditional lime-based plasters or acrylic “faux” plasters.
by Jeff Woodard
to the coarse textures of Terra and Tuscany, today’s decorative plasters span a variety of diverse designing needs. Equally as wide-ranging are opinions among decorators as to which product is more effective — traditional lime-based plasters or acrylic “faux” plasters.
“The faux plasters contain acrylic resins and filler or texturizing materials to approximate the look and feel of actual lime-based systems,” says Stephanie Bartlow of Faux Masters Studio in Yorba Linda, Calif. “The faux plasters are easier to use, but the lime-based plasters yield finishes with much more depth and dimension.”
Holly Whiting, owner of Holly Whiting Custom Painting in Hamden, Conn., sees it differently. “As a rule, acrylics have a firmer consistency than lime-based plasters, and contain no marble dust. Acrylic-based Venetian plaster as a finish is smooth, burnished to a shine. The marble dust in the plaster — even in the acrylics — allows it to burnish this way.” Unlike the properties of a joint compound, the acrylic products do not re-wet, says Whiting. “Once the plaster is dry, you can glaze over it, or pigment-wash it without re-activating the plaster.”
In choosing a Venetian plaster, knowing its ability to withstand moisture is key. A lime-based Venetian can be an excellent option for a bathroom, but its acrylic-based counterpart is not recommended for high-moisture areas, says Whiting. “Venetian plaster also requires a perfectly prepared substrate. If the wall surface is less than perfect, or drywall seams show, a Venetian plaster finish is not a good option.” In such cases, Whiting recommends a textured plaster. “It is a great choice for a wall like this, as the unevenness is part of the character of a textured finish.”
Faux Masters uses the Olde World system, which integrates natural lime with other natural materials. “The natural lime causes pigments to shift and makes the surface chalky,” says Bartlow. “It combines with the other natural materials that surface to be compressed and burnished. Those are the common characteristics of a true plaster.”
Textured products are easy to apply and compress, and the smoother products achieve a high-polished burnish. “When a textured product is paired with a smooth product over it, it produces movement and a beautiful decorative effect,” says Bartlow.
Another key factor in selecting the best product for the job is whether the surface will come into contact with ammonia-based cleaners. In those cases, the surface should be sealed. “Especially kitchen and bathroom surfaces,” says Jennifer Longworth, sales director for Sepp Leaf in New York City. Sepp Leaf manufactures Kolcaustico, a thinly applied veneer-top plaster providing a decorative surface that is fragile and can be damaged by heavy traffic.
Suedestone and Marmarino are primarily lime-based, which make them “liquid stone,” says Lily Beard, owner of The Gilded Lily Inc. in Issaquah, Wash. Suedestone features two layers of plaster tinted with glazes to increase texture, while Marmarino — typically using four or five layers to create the look of an old stone wall — is a popular choice for frescos.
On the opposite end of the scale are the rugged, cement-based Terra and Tuscany, which come in a powder form and must be mixed with water. Each, says Beard, has a rough, sand-like feel, is applied in several coats and is practical for outdoor use. “Terra is just a little more textured than Marmarino, but using Tuscany is like putting gravel onto the wall. It will turn out with deep holes and peaks.”
Venetian plasters are still popular today, but are not the favorite they once were, says Beard. “Marmarino is certainly the star. It’s just a more natural-looking finish.”
Whiting prefers any smooth plasters that are troweled on and pigment-washed. “They are so versatile. They create effects from old-world looks to rich leather appearances. Add metallic waxes, and you have an awesome finish.” Whiting does offer one note of caution for applying Venetian plaster over “green” wood: “The plaster will buckle as the wood shrinks.”
Application techniques vary, according to the composition of the material and the surface being covered. “They all need to be applied over an evenly covered wall,” notes Beard. “Whether it’s painted with water-based paint or a primer, they need an even base coat for even absorption all over. Venetian can only be applied to a level 5 wall because of its fine texture.” A level 5 surface — the highest in quality — is also best suited to Kolcaustico. “It will not fill in the roughness of a level 2 surface,” says Longworth.
Beard says all types of plaster can be applied with a trowel. “Depending on the application, whether it’s skip-troweled, side to side, up and down, there are many finishes that can be accomplished.” Most finishes require at least two layers; some take five to seven. “The results are as endless as the imagination, and each will yield a different appearance in your finish,” Bartlow says. Interesting finishes can also be attained, says Whiting, by using a spatula or roller.
Longworth says a level 5 surface is best suited for a “general finish,” which should be primed with a color similar to that of Venetian stucco. “Use a blade to apply the finish thinly, leaving little material behind. Apply three coats, allowing about 40 minutes drying time for each.” Using an electric sander and sandpaper with a grit of 250 to 350, the surface should be sanded, then wiped with a wet rag. “Repeat the application process, then sand using 800-grit paper. Re-wet the surface with a rag, wax it with Liberon Black Bison Paste Wax, and buff.”
Many plaster manufacturers offer classes in proper use of their products — and many decorators encourage would-be plaster designers to make use of them. “I hear from too many people attempting to create a finish with only half the information and without the proper techniques required to make it successfully,” says Bartlow. “It would be beneficial to become educated in the techniques required to use these products. There is a reason why people were apprenticed to create plaster finishes over the last few hundred years. It takes time to do it well.”

|