Venetian Plaster
Traditional venetian plaster consists of certain materials applied in a specific way. The material used is a lime putty containing marble flour and aged slaked lime. Premium lime from Europe is aged in underground pits, where it not only hydrates thoroughly but also absorbs trace elements from the surrounding rock.
By Gail Elber
, Venetian plastering offers the artist considerable creative scope. A skilled Venetian plasterer can produce anything from a cold, glossy, marble-like surface to a warm, antique-looking distressed effects. Yet a Venetian plaster wall is more durable than any painted surface, and a skilled plasterer’s creativity can be admired for many years to come.
Unfortunately, Venetian plaster is so appealing that a lot of painters are rushing into the field ill-prepared. Adding this technique to your repertoire requires a significant commitment of time and money for training and practice. But before you throw in the trowel, read on and see if this technique is for you.
The Egyptians, Greeks and Romans appreciated the beauty of polished lime plaster. In the 1500s, builders in Venice, trying to make buildings as light as possible so they wouldn’t sink into the mud underlying that city, enhanced lime plaster with marble dust to simulate the look of marble without the weight. The technique became known as Venetian plaster (stucco veneziano, in Italian) and was used around Europe till the early 19th century. During the 1950s and 1960s, Italian architect Carlo Scarpa made the technique popular again. Encouraging a cadre of artisans who revived and taught disused techniques, Scarpa and his disciples spread interest in Venetian plaster throughout Europe and to North America. In the past ten years, numerous schools offering training to commercial painters, fine artists and do-it-yourselfers have sprung up.
Traditional Venetian plaster consists of certain materials applied in a specific way. The material used is a lime putty containing marble flour and aged slaked lime. Premium lime from Europe is aged in underground pits, where it not only hydrates thoroughly but also absorbs trace elements from the surrounding rock. The lime and marble are ground to the fineness of talcum powder, so that the plaster can be troweled on in layers almost as thin as a paint film. Talking about Venetian plaster with your clients or suppliers can be confusing, because some companies have incorporated traditional terms such as marmorino, grassello, and even stucco veneziano into the brand names of their products. However, in general, grassello (which means “fat” in Italian) is a fine-textured lime putty designed to be applied with a flexible spatula in as many as eight to ten thin layers that are then burnished with a rigid trowel, and marmorino (“marble-like”) is a putty containing a slightly coarser marble dust that is applied using a rigid trowel. Before the advent of plastics, Venetian plaster could be applied only over a plaster or masonry wall because the substrate had to be porous for the plaster to bond with it. A few restoration specialists in Europe make their own all-natural plasters. However, modern putties for Venetian plastering contain acrylics and other polymers that allow them to stick to primed drywall. In general, the higher the acrylic content, the easier the products go on and the fewer coats they require. Lower-acrylic products produce the classic translucent effects of the medium and are applied in multiple layers.
The essential tools are a flexible stainless steel spatula for applying the material, a rigid stainless steel trowel for burnishing it and a stainless steel hawk for carrying it. The tools must be made of stainless steel so that they do not mark the plaster. Trowel edges must be kept free of nicks and dirt.
Both American and European firms make plasters designed for the Venetian technique. The material comes premixed in a can or bucket. Usually it’s supplied uncolored, although colored products are available. It can be tinted with universal tints, but if you are trying to obtain a dark color, the necessary amount of universal tint adds so much glycerin to the mix that the plaster’s setting time may become unacceptably long. You can use powdered pigments to avoid this problem. And if you’re trying to create an antique look, use natural earth pigments such as those sold by Sinopia in San Francisco; they have a warmer look than universal tints, which are colored with iron oxides. Venetian plaster’s high lime content makes it incompatible with some blue shades and metallic aluminum powder, but no problems should arise with other pigments.
Surface preparation is most important. People often assume that the multiple layers of Venetian plaster will cover imperfections, but in fact, because the surface is burnished so hard, any irregularities, such as primer drips or trowel marks in the mud, will be magnified in the finished surface, not concealed. Drywall must be finished to level 5 (taped with three layers of mud and a skim coat of drywall compound). Prime the wall with a basecoat made for the purpose, with lime paint, or with a good matte primer.
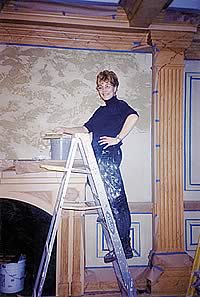
Victoria Bingham of Buon Fresco and her Venetian Plaster work. |
What happens next depends on the desired effect. From two to seven (or more) layers of grassello are applied with a spatula and then burnished when dry to the touch with a rigid trowel. Burnishing creates a glossy surface. Also, the material is translucent, and if the layers are of different colors, burnishing will create thin spots where the underlying color or colors will show through. The whole multilayered application is no more than 1⁄8 " thick.
The final layer may consist of grassello, lucido (a practically clear material), or marmorino, which has slightly larger particles. When marmorino is burnished, the trowel glides over these larger particles and produces a skip-trowel or flamelike pattern. Clear or colored grassello can be added over this layer to add depth to the effect. The more the surface is burnished, the shinier it gets. For a high gloss, it can be sanded with fine sandpaper or steel wool.
The plaster hardens over a few days as it absorbs carbon dioxide from the atmosphere. Then, the surface can be sealed with wax (wiped or troweled on) or a synthetic sealant to protect it from moisture and dirt. You may hear Venetian plaster called “faux encaustic.” This is because early lime plasters were formulated with wax, then heated with an iron after they were dry to bring a protective layer of wax to the surface. Nowadays, however, the wax is applied cold. Colored wax can be stenciled on to produce inlaid effects, or mica powder can be added to the wax for a metallic sheen.
A Venetian plaster wall is as hard as stone and the color is integral, so it is quite durable. This is a good thing, because concealing a repair in a damaged Venetian plaster wall is difficult. For little touch-ups, some of the tinted putty from the final coat must be saved in an airtight container. Some plasterers give this to the client; others store it themselves.
Though painters have a good background for working with Venetian plaster, the different medium takes some getting used to. “I recommend that new students start off small,” says instructor Bill Gauthier, who teaches classes for Sepp Leaf Products in the use of its product Kolcaustico. “Some painters come into my class and say, ‘I have this sample and a contract to do a 4,000-square-foot room.’ It’s better to start with a small entrance hall or room and work your way up.”
For one thing, tinting plasters is different from tinting paint. It takes a lot more tinting material to tint a bucket of plaster than a bucket of paint, and the wet material is much darker than the dry. If you want to use powdered pigments, mixing them is a skill all its own that you’ll have to acquire.
Also, dealing with customers during a plastering job can be harder than it is when painting. “The more complicated the surface, the more questions and anxieties come up,” he says. “Everyone has painted something themselves and knows what is involved, but with plastering, where it’s going to cost them thousands of dollars, the insecurities come out.” Gauthier prefers to work with professional designers rather than homeowners. “They know what they want, and if you’ve matched it, they sign off on what you’ve done, and convince the client.”
Another issue is the need for helpers, since you must keep a wet edge and must finish a layer the day you start it. No matter how rigorously you train together, everyone’s trowel technique will be as recognizable as their thumbprint. To counteract this, Jo LeSione of Real Illusions, appropriately based in Venice, California, moves her workers around to different parts of the wall as the job progresses so that their individual styles don’t dominate areas of the wall. “Your eye shouldn’t be drawn to a certain area,” she says. “It should look like God did it.”
To supplement divine inspiration, many suppliers of Venetian plaster materials offer training. In one to five days, students learn to apply the materials and produce various effects. But don’t plan to rely solely on classes in which you work only on sample boards. Professional applicators agree that to bridge the gap between the classroom and professional Venetian plastering, you must practice on real walls in your own shop or studio. And you’ll need to invite your helpers to practice with you.
In response to the demand for the finish and the shortage of trained plasterers, a legion of alternatives to Venetian plaster has sprung up. They contain more acrylic resins than the conventional lime plasters do, so they can be applied in fewer coats than lime plasters. If your trowel technique is sound, you can produce handsome effects with them.
However, if you yearn to make your mark in stone instead of acrylic, Olivier Garnier of Olivetti Mineral Finishes has a suggestion. “We tell novices to start out with lime paint,” he says. Olivetti’s product isn’t just watered-down lime plaster — it contains binders that allow it to be brushed on and adhere as paint. After you’ve brushed it on, you can burnish it as plaster is burnished so that underlayers show through and the surface is shiny. Cold joints aren’t a problem, so you can work alone. It’s a relatively inexpensive and user-friendly way to experiment with the possibilities of this medium and become productive quickly. Then, if you decide that Venetian plaster is for you, get some training from a master, and practice, practice, practice. When the interior of your garage looks like a palazzo, you’ll be ready to take your trowel on the road.

|